一、集成化是降低制造成本的主要途径
在控制上游原材料成本方面,永磁电机成本的最主要构成是钕铁硼等永磁材料,能够占到物料成本的 45%左右,电机控制器 30%的成本是 IGBT 模块。对于电机供应商而言,上游原材料价格波动对生产成本影响较大,根据测算,钕铁硼价格每提高 10%,电机的毛利率空间将下降 2%左右,硅钢片价格每提高 10%,电机毛利率空间下降 1%左右,2015 年年底至今,钕铁硼和冷轧无取向硅钢的价格分别累计增长 56%和 87%,相应电机的毛利率空间降低 15 个点左右。
预计未来几年稀土矿的开采量将维持在 10 万吨左右,需求侧的放量和供给侧相对紧缩的趋势有望带来永磁材料价格的小幅攀升,电机电控环节大概率将面对下游整车价格下降和上游原材料价格提升的双重挤压;而对于电机控制器供应商而言,由于 IGBT 模块目前还依赖进口,导致国内电控的成本要高出国外产品的 1.2-1.8 倍。
因此,在原材料环节,电机控制器成本的下降主要依靠核心部件国产化,目前我国已经出现了具备设计制造 IGBT 模块的公司,如株洲中车时代和比亚迪,虽然国产品牌的产品在性能上与国际知名供应商还存在较大差距,但长期来看,IGBT 模块的进口替代是大势所趋。中车的 IGBT 模块价格基本上比国外品牌低 20-30%,预计在电机控制器 IGBT 模块国产化后,电机驱动器的成本可以下降 13%-20%。
对于电机而言,上游原材料成本下降仅有两条路径,一是降低单车驱动系统的金属用量,实现驱动电机轻量化以提高功率密度,二是依靠驱动系统的高度集成简化结构,降低制造成本。对于前者而言,降低驱动系统金属用量的方法包括采用非金属的耐磨性材料替代金属结构件,如转动枢轴和一些支撑器件,或通过优化极槽比、齿槽比和定子轭高等降低单机金属用量,相关研究表明,提高电机极数能够减少每极磁通,从而减少定子轭截面积和用铁量,同时定子绕组端部缩短,用铜量也会相应降低。将电机极对数从 4 极提升至 16 极乃至 32 极,定子轭部高度依次下降 50%左右,定子铁心和转子铁心重量能够分别下降 40%和 30%,永磁铁重量由于磁极的增加略有上升,绕组重量下降 20-30%,整体电磁部件重量能够下降 32%左右,电机峰值功率密度能够提升 1 倍。按照以上结构及金属用量计算,电机物料成本 16 极将下降 17%,32 极将下降接近 30%,毛利率对应提升7-12 个点,同时能够实现 2020 年我国计划的驱动电机峰值功率密度达到 4kW/kg 的标准。
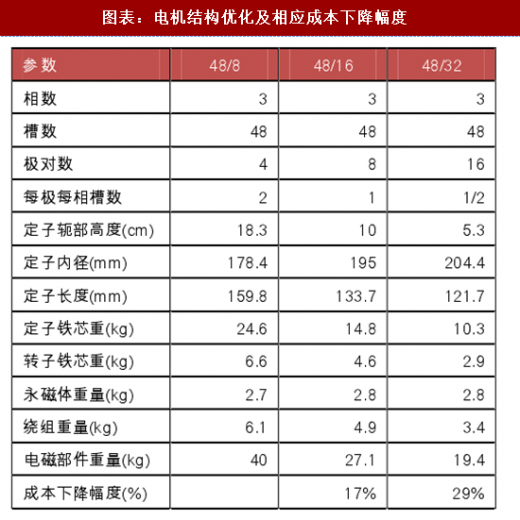
对于后者而言,电机电控的系统集成能够帮助整车厂在生产的各个阶段节省成本。首先在项目立项阶段,使用系统集成产品可以帮助整车厂实现资源整合,同时提高产品匹配度;在产品安装阶段,整车厂需要安装的动力系统点位减少,操作相对简单,能够避免由于安装不到位等因素造成的系统故障;在产品验证阶段,整车厂仅需要验证集成系统的动力性能是否达到标准,不需要再进行电机与控制器、电机与减速箱/变速箱之间的匹配度测试,节省人力物力;进入量产阶段后,集成化驱动系统帮助整车厂减少安装调试时间的效用将更加突出。同时对于电机电控供应商而言,提供集成化产品能够通过减少不必要的连接线和接插件等直接降低生产成本,据国内某电机电控供应商动力总成产品的数据,集成化产品节省的高压屏蔽线缆和接插件的预计成本在 1000 元以上,能够提高产品毛利率在 5 个点左右。
除此之外,通过技改提升生产效率旨在提高原材料利用效率,根本上是降低整体金属用量。目前国内由于制造工艺和流程的不足导致对永磁材料的原材料利用率比国外低 10%左右,假设国内厂商通过技术改造达到与国外相近的永磁材料利用率水平,目前国内纯电动车驱动电机的单车钕铁硼用量在 6kg 左右,提高整体材料利用率 10%相当于降低全部材料用量的 10%,如果按照大洋电机一年的电机产量(22705 台/年),技改后的整体钕铁硼用量将由 13.6 万 kg 降至 12 万 kg,按照当前永磁材料价格,可以计算出供应商总可下降成本将达到 400 万元左右。
二、集成化是提高单车价值量的有效途径
目前,电机电控的集成化大致可以分为两大主流方向,一是电机-变速器集成驱动系统,二是电力电子集成。对于前者而言,变速器是广泛应用于自动挡车型用来改变发动机转速和转矩的机构。电动汽车在启动、爬坡和加速等工况下,扭矩输出要求是正常行驶情况下的 4-5 倍,为了满足这些工况扭矩要求,电动汽车就不得不配备具有高倍数冗余的大功率电机,这样无疑会增加车辆制造成本和重量,因此,搭配变速器使用,可以通过变速器调速以适应不同工况要求,并减少对电机峰值扭矩的要求,提高电机利用效率,降低电机制造成本。研究表明,普通电机加两级变速器组成的一体化系统,可以将系统效率提高 5%左右,如果加入无级变速器,效率可以提高更多。国外对于电机 -变速器集成驱动系统的研究起步较早,已经研发出较多成熟产品,如麦格纳公司的 eRAD 同轴式机电耦合系统,包含驱动电机、变速器以及完全集成的电机模块和车桥断开装置,该产品已经在沃尔沃 V60 插电式混合动力汽车上成功运用;戴姆勒公司开发的集成式电驱动系统集成了驱动电机、两档变速器、电控单元及充电系统,通过对异步电机的控制完成变速器的同步换挡。
参考观研天下发布《2018年中国新能源汽车行业分析报告-市场深度分析与投资前景研究》
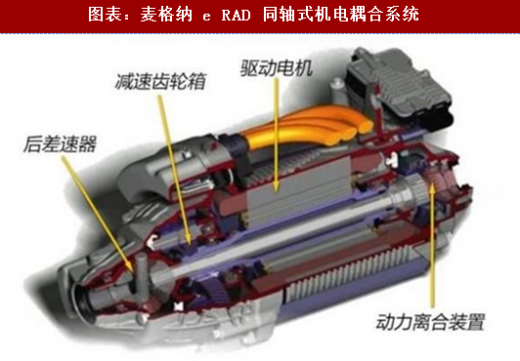
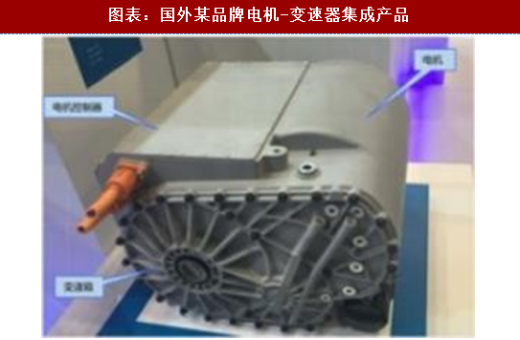
电力电子集成技术是解决目前车用变流器原材料成本高,生产成本高及功率密度小的最佳方案。较为主流的集成技术主要分为三种:单片集成、混合集成和系统集成。单片集成是采用半导体集成电路的加工方式将功率器件、驱动、控制和保护电路制作到一个硅片上,目前仅限于小功率的电力电子设备应用;混合集成式采用封装技术,将功率器件、驱动、控制和保护电路的多个硅片封装在一个模块中,具有较高的集成度,能够有效减小体积和重量,目前较为成熟的产品有丰田 Pruis 的 IPU 系统;系统集成是将多个电路和元器件有机组合成具有完整功能的电力电子系统,集成度和技术难度相对较低,多用于功率很大,结构和功能比较复杂的系统,因此是我国车用变流器最普遍采用的集成方案。目前国际汽车零部件供应商巨头如大陆、电装和博世等已经在电力电子集成技术方面取得较大突破。最为典型的例子是应用于凯美瑞、雷克萨斯混合动力轿车的丰田第三代集成控制器 THSIII,将 PCU、ECU、逆变器、升压转换器、DC—DC 转换器等全部集成,大大降低了系统的体积和重量。
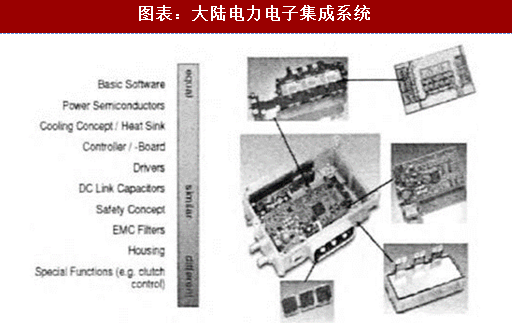
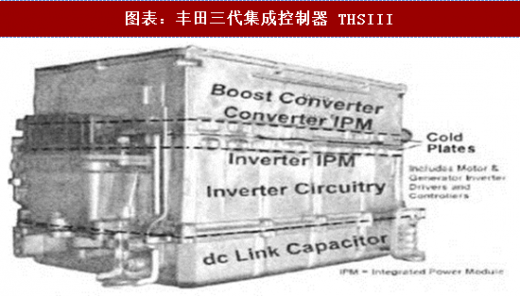
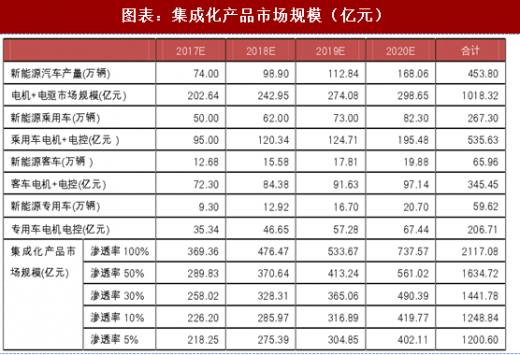
目前一些第三方电机电控供应商在动力总成方面先发制人,已经陆续研发出集成式控制器或电机电控成套产品,有效优化系统结构,减小电机电控质量体积,降低生产成本,并提高单车价值量,以实现驱动产品的量价齐升。
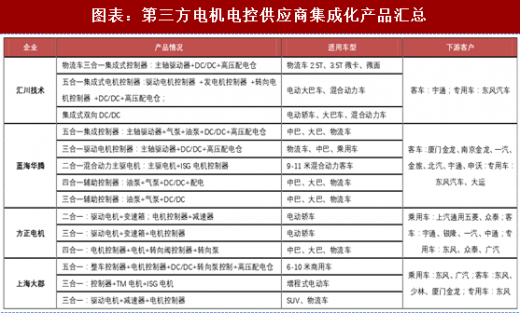
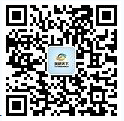
【版权提示】观研报告网倡导尊重与保护知识产权。未经许可,任何人不得复制、转载、或以其他方式使用本网站的内容。如发现本站文章存在版权问题,烦请提供版权疑问、身份证明、版权证明、联系方式等发邮件至kf@chinabaogao.com,我们将及时沟通与处理。