1 政策需求双驱动 全球大趋势确定
2017 年 5 月汽车产销情况发布,新能源汽车产销分别完成 5.1 万辆和 4.5 万辆,同比分别增长 38.2%和 28.4%。其中纯电动汽车产销分别完成 4.4 万辆和 3.9 万辆,同比分别增长52.5%和 49.0%;插电式混合动力汽车生产 0.8 万辆,销售 0.7 万辆,同比分别下降 9.3%和 28.3%。分车型来看,纯电动乘用车销售约 3.17 万辆,环比增长约 30%,同比增长约84%,其中 A 级车销量 7605 辆,同比增长 90%,环比增长 45%,A00 级车销量 1.35 万辆,同比增长 104%,环比增长 18%。插电式混合动力乘用车销售 0.63 万辆,环比增长32%,同比下滑 29%。通过同比和环比数据比较,纯电动乘用车销量有了较大提升,A级车与 A00 级车依旧延续了四月的增长。我们认为纯电动乘用车今年将是行业增长的主要来动力,市场也在由政策驱动向需求驱动过度。
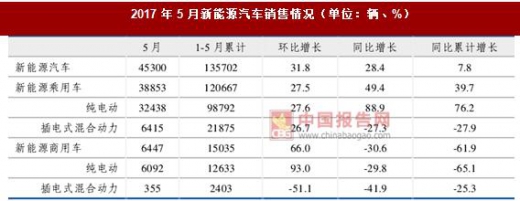
6 月 13 日工信部公布《乘用车企业平均燃料消耗量与新能源汽车积分并行管理办法(征求意见稿)》。征求意见稿披露,2018 年度至 2020 年度,乘用车企业的新能源汽车积分比例要求分别为 8%、10%、12%,超市场预期。之前市场预计积分制度延期,积分要求比例会下调。从本次办法可以发现新能源汽车积分政策将从 2018 年开始实行,对新能源乘用车产量有着较强拉动。我们测算到 2020 年新能源乘用车销量需 180 万辆以上才可满足油耗负积分抵扣, 而市场根据国家 2020 年 200 万辆新能源车目标推算乘用车 2020 年目标为 150 万,可以看到本次积分制度落地将有力推动新能源车乘用车发展。
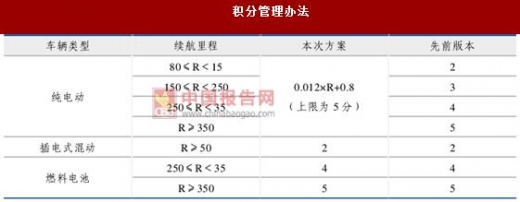
按照工信部规范,其中乘用车车型技术要求:
1)纯电动乘用车 30 分钟最高车速不低于 100km/h,纯电动模式下续驶里程不低于 100公里;2)纯电动乘用车车型,按整车整备质量(m)不同,综合工况条件下电能消耗量(Y)不满足条件①的,车型积分按照标准车型积分的 0.5 倍计算,并且积分仅限自身使用;满足条件②的,按照 1.2 倍计算;其余按照 1 倍计算。
(条件①:m≤1000kg 时,Y≤0.014×m+0.5;1000<m≤1600kg 时,Y≤0.012×m+2.5; m>1600kg 时,Y≤0.005×m+13.7;条件②:m≤1000kg 时,Y≤0.0098×m+0.35;1000<m≤1600kg 时,Y≤0.0084×m+1.75;m>1600kg 时,Y≤0.0035×m+9.59)。
2 长期逻辑关注产业升级 着眼于技术突破和成本下降
动力电池作为能量储存装置,是电动汽车的核心部件。其性能的优劣直接影响电动汽车的市场应用和普通消费者的接受度,如安全性、能量密度、功率密度、寿命以及成本等。
目前世界范围内中国的电池企业数量最多,产能最大。超过 100 家动力电池企业开展动力电池及电池系统的研发及产业化工作,超过了 1000 亿产业资金投入,形成了超过 400亿瓦时的年生产能力,技术研发及产业化进展显著。
在技术方面,我国动力锂电池的关键材料基本实现了国产化,单体技术水平与国外基本处于同一水平。已形成了较为完善的锂离子动力电池产业链体系。 我们认为,目前全球新能源车发展的制约在于动力电池能量密度和生产成本的双重压力,因此我国的补贴政策侧重点和退坡机制都在助推整个行业的产业升级,而未来的产业升级将以技术突破和成本下降为升级核心,关注产业升级也将是新能源车投资的长期逻辑。
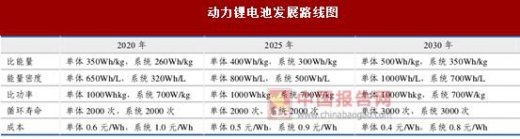
正极材料发展路线
高镍材料:高镍正极材料的产品性能和一致性仍需进一步提高,关键设备的技术水平和可靠性与国外差距较大。重点突破在包覆元素种类、包覆量对材料表面残余碱含量及电化学性能的影响,确定有利于降低残余碱含量,提高材料电化学性能的最佳包覆参数组合。提高关键设备如氧气气氛焙烧设备的技术水平和可靠性。
高电压材料:通过提高电池充电截止电压是提高锂离子能量密度最为直接有效的手段和方法,高电压材料需要大幅度提升安全性能和循环稳定性能。国内的生产线水平、品质控制水平仍存在较大差距。实现突破可对原材料逐批进行检查,对全工艺流程的各项工艺参数进行有针对性的管控,实现生产过程的智能化。
富锂氧化物固溶液材料:目前该材料的电压衰减快、倍率性能差、循环稳定性差等因素限制了其广泛应用。通过对层状富锂氧化物固溶体材料表面进行多种金属协同包覆,隔绝电解液对材料表面结构的侵蚀;通过对材料进行体相的高价金属掺杂,提高材料首次充放电效率,减少副反应的发生。
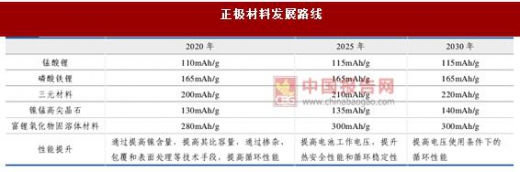
负极材料发展路线
石墨材料:我国石墨类材料的性能/价格比方面已经较日本的日立化成、三菱化学、日本碳素、JEF、昭和电工等具有优势,石墨负极的供应主要是中国企业,日本企业在材料改性方法和品质和控制方面各具特色。下一阶段的目标是进一步提升逆容量和压实密度,并降低成本。这需要表面包覆等技术提高材料加工性能和电化学性能,加强生产过程中材料的一致性和稳定性控制能力。
无定型碳材料:从产品理化参数等指标看,国内企业和国外先进企业相比,产品的性能相当。材料的主要缺陷需要改进,关键工艺技术如表面改性、材料结构调整等需要攻克。未来需要要通过包覆和掺杂等方面提高首次效率,并优化生产工艺逐渐降低成本;软碳发展趋势主要采用掺杂、修饰等改性处理,提高其比容量。
硅碳材料:目前国内外不少负极材料生产企业均已开始布局硅碳负极的开发与商业化,但大部分处于研究阶段和小规模批量化生产阶段。主要在于关键工艺技术如纳米化技术、材料结构构筑等需要进一步提高。下一阶段目标,在保持高比容量的前提下,进一步提高其库伦效率、循环性能,并逐步降低成本。
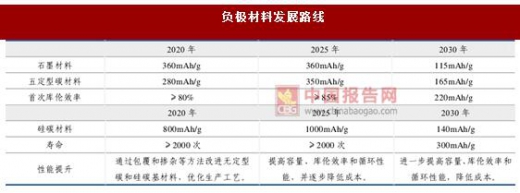
隔膜技术发展规划
根据发展目标,2020 年将实现高品质 PE 隔膜、PP 隔膜的规模化生产,高品质陶瓷图层隔膜的规模化生产及相关装备的国产化;2025 年,高安全性复合隔膜的规模化生产;锂离子导电涂层复合隔膜的产业化,耐高压隔膜的产业化。2030 年,高安全性、耐高压的高性能隔膜规模化生产;固体电解质的产业化。
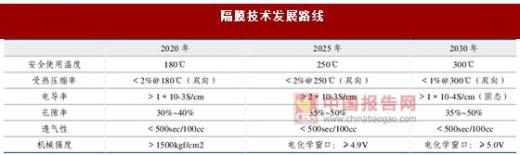
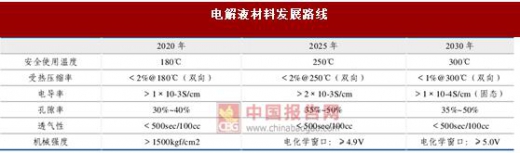
目前我国企业关于产业布局,杉杉股份、当升科技已经开始布局研究和生产高镍三元材料。星源材质、上海恩捷(创新股份)已经具备比较强的湿法涂覆产品。我们认为行业已经逐步迈过了资金壁垒,企业纷纷在跑马圈地努力构建客户壁垒,在争抢客户的过程中也会带来电池降价的趋势,中小厂商的生产压力会激增。长期看能够助推技术突破的企业将是具备大资金量、高技术水平的企业,而成本下降取决于规模化生产后企业的管理水平。因此我们认为长期龙头企业的盈利水平的差异性将会比较显著。
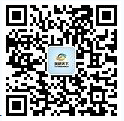
【版权提示】观研报告网倡导尊重与保护知识产权。未经许可,任何人不得复制、转载、或以其他方式使用本网站的内容。如发现本站文章存在版权问题,烦请提供版权疑问、身份证明、版权证明、联系方式等发邮件至kf@chinabaogao.com,我们将及时沟通与处理。