导读:转向节热处理后表面要清理氧化皮,任何部位不允许有裂纹、折叠等缺陷。由于该锻件有效厚度差别较大,热处理淬火有开裂倾向。如果使用油压机更为方便,因为在油压机制造时,要改变滑块行程是件很容易的事。在沃尔沃锻造厂,由于切边模具制造相当精确,卧式转向节切边后,不需要进行校正工序。
中国汽车零部件再制造行业竞争态势及投资方向调研报告(2013-2017)
中国蓄电池市场供需调研与前景分析报告(2013-2017)
考虑到汽车转向节的工作条件和重要性,转向节材料,一般使用中碳低合金钢,常用42CrMo 方型或圆型热轧钢,或相当于42CrMo 的材料,也有少数厂家使用 40Cr。无论哪一种转向节,都是由叉部、盘部和杆部组成,现在有一些转向节还增加了转向臂和横拉杆臂,结构更为复杂。转向节各部截面相差悬殊。叉部左右不对称,杆部细而长,长径比约为 4,占转向节总高度的2/3。从整个形状看,叉部和杆部有一定的夹角。锻造的关键在于,终锻前制坯必须合理,这样才能满足终锻成形要求。
1 立式锻造工艺
以斯太尔转向节为例:锻件材料42CrMo,锻件重 32kg,杆长 220mm,锻件技术条件要求符合 DIN7526E 级标准。两班制生产,全年需求量400000 件,属中型锻件特大批量生产。根据斯太尔转向节的的形状,只能采用立式锻造。从工艺的先进性、可靠性和操作自动化诸因素分析,闭式挤压工艺最为先进,工艺质量稳定、生产可靠、班产量高,同时便于实现机械化操作。因此,确定工艺流程:镦粗—闭式挤压—预锻—开式终锻。
由于转向节锻件重量较大,锻造设备工作台面较宽,操作距离长,故转向节锻造工序采用两台机械手操作。当加热后的坯料出炉到达指定位置,第一台机械手把热坯料送到压力机第一工位进行镦粗,镦粗的目的是清除氧化皮,镦粗后再由第一台机械手夹起,翻转 90°送到第二工位。第二工位是挤压工序,挤出部分杆部和叉部。挤压模具上下设有顶出装置,闭式挤压的变形力为45000kN左右。
挤压工序完成以后,第二台机械手伸入,夹起锻件,送到第三工位进行预锻。预锻的目的是分配金属,使转向节的各部分基本成形,其变形力在40000kN 左右。此后再由第二台机械手把锻件送到第四工位进行终锻。终锻变形力略低于预锻力。
整个锻造生产采用机械手操作,生产效率比锤上高得多,也比没有机械手方便得多,同时也减少了操作人员,减轻了工人的劳动强度,提高了生产效率。目前,世界上有百余条25000kN~63000kN热模锻压力机转向节生产线(或机组)。
中国重汽锻造厂转向节的挤压工艺已经达到国际水平,在国内也有许多生产厂家采用此工艺。
关于在生产中是否使用机械手问题,要据具体情况而定,当然全自动化,高起点的生产线最好,但在很多情况下,机械手也有不如人工操作的时候,因此,设计生产线不一定要全自动化,就是在先进的工业国家也是如此。在瑞典 VOLVO 锻造厂,160000kN热模锻压力机生产线是全自动化,而40000kN 生产转向节还是手工操作。锻造生产自动化问题要根据产量、质量、安全生产、效益诸方面考虑。从近二十年的生产经验来看,对斯太尔汽车转向节而言,如在工艺和设备做某种改动以后,镦粗工序和预锻工序可以省去。这样整个生产过程就缩短一半。目前,这条生产线,每分钟生产一个锻件,如把电炉加大一些,使用2000kW~3000kW 电炉,一分钟生产两件到三件是可能的,产量会翻一翻。
2 卧式锻造工艺
有些汽车的转向节由于形状的原因,只能采用卧锻的方法完成。过去国内热模锻压力机卧锻生产汽车转向节工艺采用压扁—二次(调头,翻转 90°)压扁—预锻—终锻成形。生产效率较低,工人劳动强度较大。
。瑞典沃尔沃锻造厂锻造的转向节,材料 42CrMo,卧式锻造工序为:闭式预锻—开式终锻。沃尔沃锻造厂锻造转向节使用美国克林宁公司生产的 40000kN 热模锻压力机。加热后坯料由滑道传到指定位置后,人工夹起坯料放到闭式预锻模中,压力机压下完成预锻工序,然后人工翻转放入终锻型槽,压力机最后锻造成形。终锻型槽水平分模,人工把成形的转向节送出压力机,锻件通过输送带送到切边工位进行切边。每分钟生产三件,生产速度快,整个锻造生产人工操作,过程简单。
闭式挤压的变形力为44000kN 左右,终锻变形力在40000kN左右。瑞典技术人员自己承认使用40000kN 压力机生产转向节,吨位偏小,设备工作超负荷,但仍在设备安全系数之内,如选63000kN 热模锻压力机更好。
观察转向节锻件,毛边分布不均匀,杆部尾端飞边很小,但产品成形好,说明金属材料的分配尚好,但不富裕。在热挤压过程中,立式挤压和卧式挤压的模具是不同的,立式挤压是先挤转向节杆的尾部,而卧式挤压则是先挤杆的根部。
沃尔沃锻造厂坯料加热后,没有清氧化皮工序,从锻件上看氧化皮很少,这说明他们的加热速度很快, 时间很短,形成氧化皮很少,加热炉功率2500kW~3000kW。估计他们在加热过程中采用了还原性气体。沃尔沃重型汽车转向节杆部不太长,约在220mm 左右。但现在汽车行业中还有一种汽车的转向节的杆部比较长,虽然这种汽车数量比较少见,但也代表一个方面。象杆部很长的转向节在闭式挤压前,如果没有一个制坯工序,它的杆部很可能挤不出来,因此,增加一个成形镦粗或拍扁工序是有必要的。但是否保留成形镦粗或拍扁工序,还得根据具体情况而定。
典型的带有转向臂的转向节,除了具备一般转向节的特点外,还多了一只臂。根据其几何形状,多数采用立式锻造成形工艺。也有少数采用卧式锻造的方法。由于形状复杂,金属分配更困难,一道闭式挤压工序几乎不能使金属分配达到理想的要求,因此,很多情况下,要设置成形镦粗或制坯工序。采用三道工序完成:第一制坯工序,第二闭式挤压,第三终锻成形。制坯工序不仅要清除氧化皮,更重要的是进行金属材料的初次分配,为闭式挤压做准备工作;闭式挤压的目的是进一步分配金属,使闭式挤压后的锻坯接近锻件形状;终锻只是使毛坯达到图纸要求的过程。
转向节在 25000kN 热模锻压力上锻造,坯料加热后,通过滑道送到压力机旁,由人工夹起放入第一工位进行成形镦粗,此时主要完成叉部的金属分配,同时又为挤压杆部和转向臂聚集金属。然后下顶杆顶出锻件,由人工将坯料翻转 90°送到第二个工位,作闭式挤压,完成转向臂的金属分配,为杆部的成形储备金属,此时杆部仍未完全成形。挤压工序的变形力约在18000kN 左右;然后人工再将坯料送到第三道工位,压力机使杆部、转向臂和叉部全部成形,完成锻造工序。整个锻造过程一火完成,时间约半分钟。在这三个工序中,成形镦粗和挤压工序的设计思想是每一道工序完成转向节的一个部位金属分配,同时又为下一道工序的金属成形做材料储备。成形锻件由人工推出压力机,传送带送切边工序。
后续锻造工序
(1)切边工序(以斯太尔转向节为例)斯太尔转向节的切边和校正在一台设备上完成,人工操作。切边力约2000kN左右,校正力约在4300kN左右。
切边模凹模在上,凸模在下,切边时,带飞边的锻件放在凸模上,凹模下行切掉飞边,凹模中的顶出机构将转向节从凹模中顶出。下置凸模与锻件是平面接触,贴合面非常好,切边时锻件不动,凹模和毛边上、下运动。因此,锻件变形小。卧式转向节切边工序:为减小切边变形力,切边凹模设计为梯形结构。
(2)校正工序(以斯太尔转向节为例)斯太尔转向节校正工序的目的是校正转向节盘部和杆的几何关系。由于切边模的凹模倒置,转向节主要变形在盘部,故校正模的设计以压平盘部为主。校正后的转向节在料箱内进行堆冷。
立锻切边和校正工序一般设计在一台设备上,吨位在 5000kN~8000kN。由于切边和校正的行程比较大,所以标准规格的曲柄压力机的行程空间不够,需要改变设备参数,加大曲柄的尺寸,随之切边压力机要做一系列的改动,比较麻烦。如果使用油压机更为方便,因为在油压机制造时,要改变滑块行程是件很容易的事。在沃尔沃锻造厂,由于切边模具制造相当精确,卧式转向节切边后,不需要进行校正工序。
(3)转向节锻后对热处理要求(以斯太尔转向节为例)
转向节锻造和热处理密切相关,转向节金属组织关系到整车安全性和可靠性,因此,锻造要对热处理提出技术要求。以斯太尔转向节为例来阐述对转向节锻件的热处理要求:斯太尔转向节锻后不需进行正火处理,直接进行调质处理。沃尔沃转向节也是直接进行调质处理。斯太尔转向节调质后要求抗拉强度 880MPa~1030MPa,在杆部规定的位置取样。为了达到节能目的,锻造后冷却到 200℃以下,即可加热进行淬火处理。为了确保调质质量,一般情况下不允许进行余热淬火。调质处理后硬度为 261~304HB;金相组织按GB/T13320评级,边部1~4级,心部允许5~6 级。表面脱碳层深度,加工面不得超过实际加工余量的一半,非加工面单边不得大于1mm。
转向节热处理后表面要清理氧化皮,任何部位不允许有裂纹、折叠等缺陷。由于该锻件有效厚度差别较大,热处理淬火有开裂倾向。
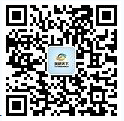
【版权提示】观研报告网倡导尊重与保护知识产权。未经许可,任何人不得复制、转载、或以其他方式使用本网站的内容。如发现本站文章存在版权问题,烦请提供版权疑问、身份证明、版权证明、联系方式等发邮件至kf@chinabaogao.com,我们将及时沟通与处理。