1、 溅射靶材行业市场空间广
根据统计,2015 年全球半导体材料销售额为435 亿美元,其中晶圆制造材料销售额为242 亿美元,封装材料为193 亿美元。在晶圆制造材料中,溅射靶材约占芯片制造材料市场的2.6%。在封装测试材料中,溅射靶材约占封装测试材料市场的2.7%。从2011-2015年,世界半导体用靶极溅射材料市场从10.1亿美元,增长至11.4亿美元,复合增长率为3.1%。2016年全球半导体材料市场销售额达到443亿美元,同比增长2.4%,其中晶圆制造过程中涉及半导体材料市场份额达到247亿美元,同比增长3.1%,封装测试过程涉及半导体材料达到196亿美元,同比增长1.4%。受半导体行业整体增长驱动,靶极溅射材料市场持续增长,预计2017年,全球集成电路用溅射靶材量将达到13.4亿美元,其中晶圆制造用溅射靶材市场将达到7.3亿美元,封装测试用溅射靶材将达到6.1亿美元。2015 年,我国集成电路用溅射靶材市场规模为11.6亿元,2016年国内半导体用溅射靶材市场规模突破14 亿元。
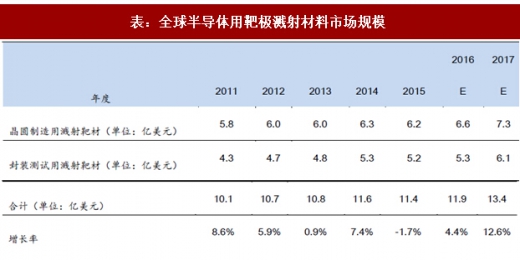
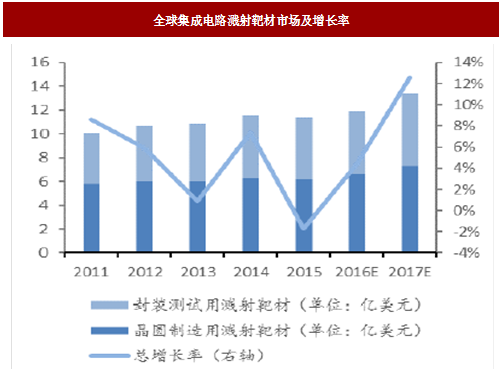
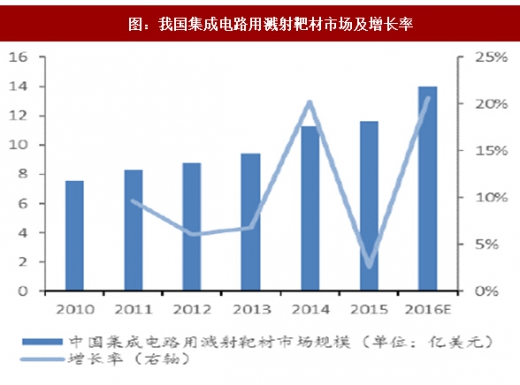
参考观研天下相关发布的《2017-2022年中国金属靶材行业市场发展现状及十三五发展趋势前瞻报告》
2、 溅射靶材产品多样,技术壁垒深
半导体晶圆制造中成膜方法主要包括物理气相沉积(PVD)和化学气相沉积(CVD)。溅射镀膜法属于PVD的一种,其作用原理是辉光放电过程:在真空放置室内设计正负两极,通入压强为0.1Pa~10Pa的氩气(Ar),在外加高电压条件下,实现节点区域Ar的击穿,形成气体离子,此时带电荷的气体离子在正负极间电场作用下实现迁移,带正电荷离子加速向负极撞击,从而导致负极表面金属原子获得能量溢出,此过程称为物质的溅射,溢出的金属原子在所需基底上形成均匀的薄膜,半导体的制备过程初期就是利用此类溅射实现晶圆电极的制备。后期,在此基础上,引入了与电场方向正交的磁场,磁场作用是使得Ar+溅射后产生的二次电子在洛伦兹力的作用下实现圆形轨迹运动,从而提高了二次电子与Ar分子接触的概率,形成更多Ar+而增强辉光放电效应,此类技术由于引入磁场,因此被称之为磁控溅射。
在磁控溅射过程中,为保证溅射效果均匀,靶极材料一般以匀速旋转,由此可见此类技术靶极材料作为薄膜的材料源,属于耗材。同时,为获得高纯薄膜,对靶极材料纯度的要求一般较高,金属材料纯度达到99.99%以上。
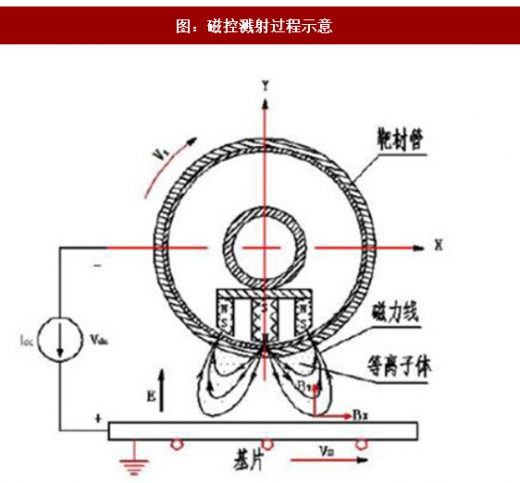
2.1、 溅射靶材产品多样
靶极按照成分不同可分为金属靶极(纯金属铝、钛、铜、钽等)、合金靶极(镍铬合金、镍钴合金等)和陶瓷化合物靶极(氧化物、硅化物、碳化物、硫化物等),半导体晶圆制造中200nm(8寸)及以下晶圆制造通常以铝制程为主,使用的靶材以铝、钛元素为主。其中高纯铝的导电性比铜和硅差一些,但铜存在与硅接触电阻率高,并且扩散进入器件引起器件性能差。铝的电阻率达到2.7μΩcm,对起初作为阻挡层的二氧化硅有足够低的电阻率,靶极原料可被提纯到5~6个“9”的纯度。在半导体硅表秒起初通过氧化过程生成SiO2作为阻挡层,降低硅表面与上层之间的阻抗,阻止铝和硅之间形成合金,在铝与第二层铝之间蒸镀一层绝缘(IMD)作为介电层,介电层材料一般选用氧化物、氮化硅或聚酰亚胺,IMD层通过光刻技术形成新的连接孔(via)或塞(plug),重复IMD/塞/金属沉积或光刻图形化工艺的重复最终形成多层系统。200nm制程中阻挡层金属一般使用钛钨(TiW)、氮化钛(TiN),TiN层可以通过溅射形成,也可以溅射Ti后再N2或NH3的气氛下,通过600℃形成热氮化层,在TiN层下溅射一层Ti,提高与硅衬底建导电率。
300nm(12寸)晶圆制造,多使用先进的铜互连技术,主要使用铜、钽靶材。为了确保众多细小布线的质量,必须提高镀铜薄膜均匀性。以前99.995%(4N5)的靶材纯度可以满足0.35μmIC的工艺要求,现在99.9999%(6N)的靶材纯度才能满足制备0.18μm线条的工艺要求。在20世纪90年代IBM公司引入铜基大马士革工艺,从而实现取代铝的金属化并应用在300nm晶圆制造中。原因是铝电阻率高于铜,信号速度需要提升,导电性铝不足,同时12英寸大硅片的制造需要更长和更细的金属线,同时via数量增加导致电阻进一步加大,因此金属层转向电阻率仅为1.7μΩcm的铜,同时在金属与金属之间采用低k值得到IMD从而实现提高性能和减少要求的金属层数。300nm制程中一般使用钽(Ta)、TiN和氮化钽(TaN)。溅射中可直接应用金属靶极或在Ta表面通过高温N2或NH3条件下生成。
难熔金属中钨(W)和钼(Mo)因为提供了低的接触电阻在大规模和超大规模集成电路要求中的接触孔和更大的门阵列芯片的表面接触面积占比成为可能,同时W具有高熔点、高导电性、高抗电移性、逸出功接近于硅的频带隙和良好的热稳定性等特点,Mo具有高熔点、高电导率、较低的比阻抗、较好的耐腐蚀性和良好的环保性能等特点,因此W和Mo逐步被应用于VLSI和ULSI的替代铜、铝的导电层中。
2.2、 溅射靶材制造工艺技术壁垒高
金属靶材的制备中包括材料纯化和靶材制备两个过程。纯化过程中确保降低靶材中杂志含量,制备过程确保靶材表面平整程度。
材料纯化过程中主要方法包括化学提纯化和物理提纯法。化学提纯法分为湿法提纯和火法提纯,湿法提纯包括离子交换、溶剂萃取、置换沉淀和电解精炼等;火法提纯包括氯化精馏、碘化热分解、金属有机物热分解、歧化分解、熔析精炼和熔盐电解等。目前应用最多的是电解精炼提纯,其原理是在电解过程中,利用杂质金属和主金属在阴极上析出电位差异从而达到提纯目的。常见的如高纯Cu、Co、Ni、Ag和Ti。
物理提纯法利用主体金属与杂质物理性质差异,采用蒸发、凝固、结晶、扩散、电迁移等物理过程去除杂质,具体方法包括区域熔融法、偏析提纯法、真空蒸馏法、单晶法和电迁移法,一般此类提纯在真空条件下进行,一些吸气性很强的金属需要在高正空和超高真空条件下完成提纯,其原理是在此条件下降低气体分子在金属中溶解度从而实现提纯,对于低熔点的Al、Cu、Au和Ag等金属及其合金等采用真空感应熔炼制备;对于高熔点的Ti、Co、Ta和Ni等金属采用真空电子束炉或电弧熔炼制备。
工业中通常使用物理提纯和化学提纯相混合的方法制备电子级金属材料,例如工业中电子级Al的制备是利用铝土矿(Al2O3、SiO2和Fe2O3)在过量盐酸条件下过滤,在过量NaOH条件下过滤,溶液通入过量CO2生成Al(OH)3,Al(OH)3灼烧后生沉淀过滤得到Al2O3,电解Al2O3后得到高纯Al,纯度达到4N9,利用高纯铝作为阳极,NaF2Al(C2H5)3配合物溶解在甲苯(CH3C6H5) 中,配合物含量为50%作为电解液,采用高纯Al作为阴极进行电解,得到纯度4N5的高纯铝。工业中电子级Cu的提纯过程中首先采用物理提纯法重结晶和化学提纯法离子交换法制备高纯的硫酸铜电解液,用湿法电解硫酸铜溶液制备高纯阴极铜,通过高纯熔炼去除原料中C、N和O等气体元素,最终得到高纯铜锭。工业中制备电子级钛有多种方法。目前实现工业化的包括Kroll法(Mg还原法)和Hunter法(Na还原法),碘化法和电子束熔融精炼法。利用钛矿将电炉熔炼制取钛的氧化物,通过氯化工艺利用TiO2在Cl2和C反应得到纯TiCl4,将液体TiCl4注入装有金属还原剂的钢制容器中进行还原反应,排出大部分副产的氯化物后,以真空蒸馏法除去剩余的氯化物和未反应完全的金属还原剂,氯化物通过熔盐电解产生Cl2和金属还原剂,从而实现循环利用,Kroll法使用Mg做还原剂,Hunter法使用Na做还原剂,在制备高纯度的TiCl4中,通常采用多级精馏的方法除去其中高沸点和低沸点的杂质;碘化法是利用利用钛在低温区与高温区与碘的可逆反应,将纯度低的钛材料与碘一起填充于密闭容器中,在低温区碘化反应生成四碘化钛,四碘化钛扩散至高温区,在钛细丝或钨丝上发生热分解反应,析出高纯钛,达到6N级别。
靶极溅射制备按工艺可分为熔融法和粉末冶金两大类。高纯金属如Al、Ti、Ni、Cu、Co等具有良好塑性,使用熔融法制备,将一定成分配比的合金原料熔炼( 电子束或电弧、等离子熔炼等),再将合金熔液浇注于模具中,形成铸锭,最后将得到的锭进行热处理和机械加工,制成靶材。为保证铸锭中杂质元素含量尽可能低, 通常其冶炼和浇注在真空或保护性气氛下进行。但铸造过程中, 材料组织内部难免存在一定的孔隙率, 这些孔隙会导致溅射过程中的微粒飞溅, 从而影响溅射薄膜的质量。为此, 需要后续热加工和热处理工艺降低其孔隙率。通常该法制备的靶材杂质含量(特别是气体杂质含量)低,密度高,可大型化生产;但是仍存在靶材晶粒尺寸和晶粒织构取向均匀性较难控制的缺点。
对于W、Mo和R等难熔金属及合金,通常采用粉末烧结法制备溅射靶极。粉末冶金法是将一定成分配比的合金原料熔炼, 浇注成铸锭后再粉碎, 将粉碎形成的粉末经等静压成形, 再高温烧结, 最终形成靶材。常用的粉末冶金工艺包括冷压、真空热压和热等静压等。粉末冶金法适合于难熔金属如钨、钼靶材及陶瓷靶材的制备。优点是靶材成分均匀,可获得超细晶粒;缺点是杂质含量高,同时密度低,容易造成微粒飞溅。
高纯溅射靶材是伴随着半导体工业的发展而兴起的,研发生产设备专用性强,涉及测试平台精密度高。全球半导体工业的区域集聚性造就了高纯溅射靶材生产企业的高度聚集。溅射镀膜工艺起源于国外,西方国家投入较早。目前,全球溅射靶材研制和生产主要集中在美国、日本少数几家公司。以霍尼韦尔(美国)、日矿金属(日本)、东曹(日本)等跨国集团为代表的溅射靶材生产商较早涉足该领域,经过几十年的技术积淀,凭借其雄厚的技术力量、精细的生产控制和过硬的产品质量居于全球溅射靶材市场的主导地位,占据绝大部分市场份额。目前,我国主要是宁波丰电子、有研亿金,福建阿石等企业在国内占据少量市场。
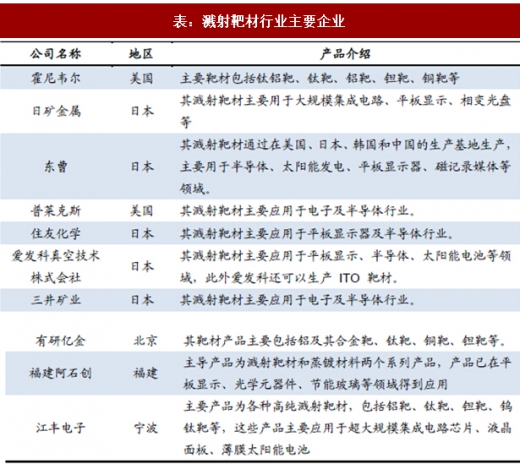
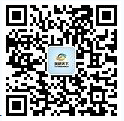
【版权提示】观研报告网倡导尊重与保护知识产权。未经许可,任何人不得复制、转载、或以其他方式使用本网站的内容。如发现本站文章存在版权问题,烦请提供版权疑问、身份证明、版权证明、联系方式等发邮件至kf@chinabaogao.com,我们将及时沟通与处理。