靶材因其成分、形状和应用领域不同,可以采用不同的分类方法。
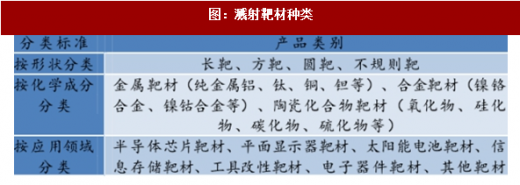
靶材主要应用在半导体、平面显示、太阳能电池等领域。其主要性能表现在纯度、杂质含量、密度、均匀性、尺寸等方面。因应用领域不同靶材对金属材料的选择和性能要求存在着一定的差异,通常来说半导体靶材纯度最高,制作工艺最为复杂,平板材料次之,太阳能电池材料标准最低。
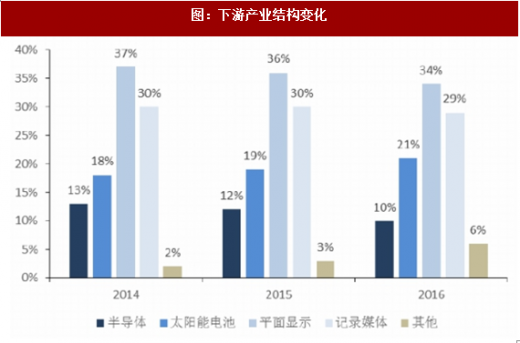
半导体靶材是晶圆制造重要的原材料,主要以铜靶、铝靶、铁靶和担靶等为主。半导体芯片行业历经半个世纪,目前仍遵循着“摩尔定律”向前发展。在晶圆制造方面,芯片尺寸不断减小(目前主流28纳米以下),同时晶圆尺寸不断增大以进一步降低成本(目前12英寸是主流)。在集成电路领域主要应用在晶圆制造和先进封装过程中。为了满足半导体芯片高精度、小尺寸的需求,芯片制造对溅射靶材纯度要求很高,通常需达99.9995%C5N5)甚至99.9999%C6N)以上,这在各下游应用中要求是最高的,价格也最为昂贵。
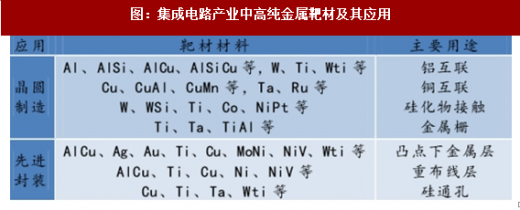
平板显示镀膜用溅射靶材主要品种有:铝、铝合金、铂、铬、铜、铜合金、硅、铁、锐和氧化锢锡CITO)等。平面显示面板的生产工艺中,屏显玻璃基板要经多次溅射镀膜形成ITO玻璃,然后再经过镀膜、加工组装用于生产LCD面板、PDP面板及OLED面板等。对于触控屏,则还需将ITO玻璃进行加工处理、经过镀膜形成电极,再与防护屏等部件组装加工而成。此外,为了实现平板显示产品的抗反射、消影等功能,还可以在镀膜环节中增加相应膜层的镀膜。平面显示行业一般要求靶材纯度达99.999%C5N)以上。
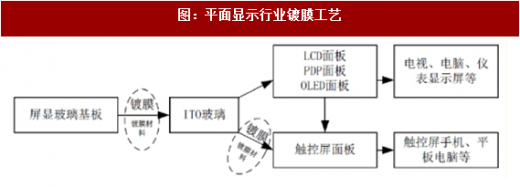
太阳能电池用溅射靶材主要品种有铝、铜、铂、铬、氧化锢锡CITO),氧化铝锌(AZO)等。太阳能电池主要包括晶体硅太阳能电池和薄膜太阳能电池。目前,PVD镀膜工艺主要应用于制备薄膜太阳能电池,靶材纯度一般要求4N以上。其中,铝靶、铜靶用于导电层薄膜,铂靶、铬靶用于阻档层薄膜,ITO靶、AZO靶用于透明导电层薄膜。
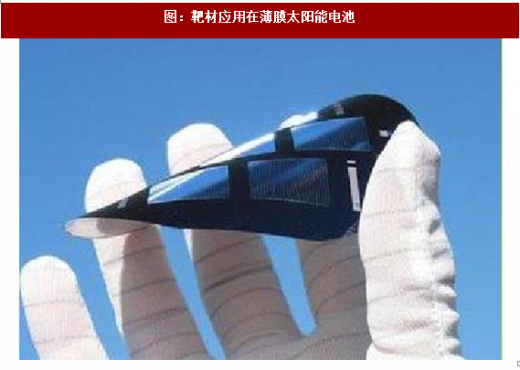
靶材的制备方法
溅射靶材在制备技术上按生产工艺可分为熔融铸造法和粉末冶金法两大类。在靶材制备过程中,在严格控制纯度、致密度、晶粒度、结晶取向的基础上,通过选择不同的热处理工艺及后续成型加工过程以确保靶材的质量。
参考观研天下发布《2016-2022年中国ITO靶材产业现状分析及十三五发展策略分析报告》
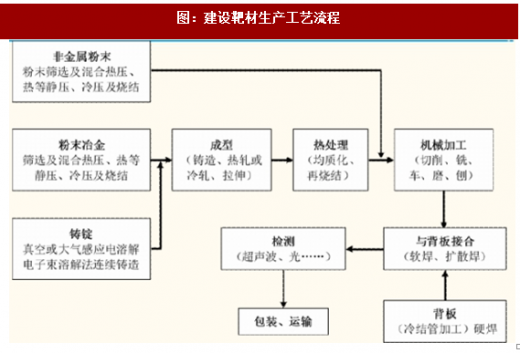
(1)熔融铸造法
熔融铸造法是制备磁控溅射靶材的基本方法之一,常用的熔炼方法有真空感应熔炼、真空电弧熔炼和真空电子轰击熔炼等。高纯金属如AI,Ti,Ni,Cu,Co,Ta,Ag,Pt等具有良好的塑性,直接在原有铸锭基础上进一步熔铸后,进行锻造、车匕制和热处理等热机械化处理技术进行微观组织控制和坯料成型。与粉末冶金法相比,熔融铸造法生产的靶材产品杂质含量低,致密度高,但材料内部存在一定孔隙率,需后续热加工和热处理工艺降低其孔隙率。
(2)粉末冶金法
对于难熔金属靶材、熔点和密度相差较大的多种金属合金靶材、无机非金属靶材、复合靶材的制备而言,熔融铸造法无能为力,需要采用粉末冶金法。粉末冶金工艺首先进行粉体材料的预处理,包括采用粒度和形貌合适的高纯金属粉末进行均匀化混合、造粒等,再选择合适的烧结工艺,包括冷等静压CCIP)、热压(日P)、热等静压(HIP)及无压烧结成型等。其关键在于:选择高纯、超细粉末作为原料;选择能实现快速致密化的成形烧结技术,以保证靶材的低孔隙率,并控制晶粒度;制备过程严格控制杂质元素的引入。粉末冶金工艺还具有容易获得均匀细晶结构、节约原材料、生产效率高等优点。
靶材行业的生产的技术壁垒
高纯溅射靶材行业是典型的技术密集型行业,要求业内厂商具有较强的技术研发实力和先进的生产工艺,具有完善的品质控制能力。其主要技术门槛表现在以下几个方面。
纯度和杂质含量控制是靶材质量最重要的指标。靶材的纯度对溅射薄膜的性能有很大影响。若靶材中夹杂物的数量过高,在溅射过程中,易在晶圆上形成微粒,导致互连线短路或断路。
靶材的成分与结构均匀性也是考察靶材质量的关键。对于复相结构的合金靶材和复合靶材,不仅要求成分的均匀性,还要求组织结构的均匀性。
晶粒晶向控制是产品研发主要攻克的方向。溅射镀膜的过程中小的溅射靶材受轰击时,由于靶材内部孔隙内存在的气体突然释放造成大尺寸的靶材颗粒或微粒飞溅,或成膜之后膜材受二次电子轰击造成微粒飞溅,这些微粒的出现会降低薄膜品质。例如在极大规模集成电路制作工艺过程中,每150mm直径硅片所能允许的微粒数必须小于30个。怎样控制溅射靶材的晶粒,并提高其致密度以解决溅射过程中的微粒飞溅问题是溅射靶材的研发的关键。
靶材溅射时,靶材中的原子最容易沿着密排面方向优先溅射出来,材料的结晶方向对溅射速率和溅射膜层的厚度均匀性影响较大,最终影响下游产品的品质和性能。需根据靶材的组织结构特点,采用不同的成型方法,进行反复的塑性变形、热处理工艺加以控制。
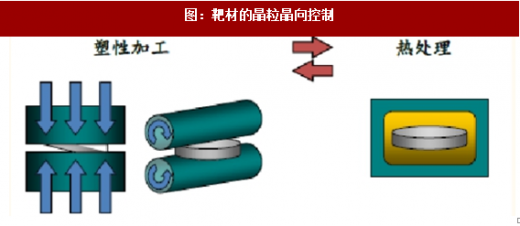
金属精密加工和外形控制直接影响下游客户的使用效果。用于靶材溅射的机台十分精密,对溅射靶材的尺寸要求很高,这对靶材厂商的金属加工精度和加工质量提出了很高的要求,如表面平整度等。例如,靶材粗糙化处理可使靶材表面布满丰富的凸起尖端,这些凸起尖端的电势将大大提高,从而击穿介质放电,但过大的凸起对于溅射的质量和稳定性是不利的。
随着薄膜技术的发展、芯片性能的提升,对配套溅射靶材在纯度、微观结构、可靠性等方面提出了越来越高的要求。集成电路产业60年代起源于美国80年代行业重心转向日本,90年代又转向韩国、台湾。因而在靶材生产方面日、美靶材企业得以与Intel、旧M等微电子巨头一起调试工艺,推进薄膜制备技术发展,具有很大的技术和品牌优势。与之相比,虽然近年来半导体产业加速向我国转移,国内半导体产业正在迎来黄金期,但总体而言我国半导体行业尤其是中上游的电子化学品、化学材料产业仍处于起步阶段。而我国一些靶材生产商是冶金材料企业,对半导体企业等使用方的实际需求很难做到“量体裁衣”。这也要求国内靶材厂商对客户实际需要进行深刻、透彻的研究,与使用方一起完善工艺。随着国内下游半导体、平面显示产业的发展,电子化学品需求量巨大,进口替代空间广阔,国内靶材企业有很大的发展空间。
资料来源:观研天下整理,转载请注明出处(ZTT)
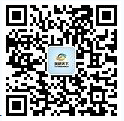
【版权提示】观研报告网倡导尊重与保护知识产权。未经许可,任何人不得复制、转载、或以其他方式使用本网站的内容。如发现本站文章存在版权问题,烦请提供版权疑问、身份证明、版权证明、联系方式等发邮件至kf@chinabaogao.com,我们将及时沟通与处理。