(1)飞机机身结构件发展概述
一百多年来,飞机设计和制造能力取得了巨大的进步,尤其是两次世界大战及冷战阶段军备竞赛对航空工业的发展起到了极大的促进作用,推动了大量关键技术的开发及应用。
飞机选材、用材的思想和原则主要受到飞机整体设计思想演变的影响。早期的飞机设计仅考虑到飞机的静强度要求,在设计中引入安全系数,使用载荷乘以该安全系数后作为设计载荷,所设计构件的工作应力应低于构件选材的许用应力,即在设计载荷下不发生结构破坏,在使用载荷下不产生永久变形。这种静强度设计思想要求结构材料要具有高强度和高模量指标。随着飞机低空高速飞行的要求越来越高,飞机结构在保证静强度的同时必须由足够的刚度,以克服大表速引起的静、动气动弹性问题。1954 年英国“彗星”号飞机空中解体事故引起了飞机设计思想的革命性转变,设计界改变了单纯追求材料强度的倾向,开始重视材料的疲劳性能,强调材料的韧性和抗应力腐蚀性能。铝合金和高强度钢可以满足机体结构的静强度与刚度要求,但在韧性和抗应力腐蚀方面,钛合金是更好的选择,从美国近三十年空军战斗机选材上可以看到这一趋势:

钛合金的使用是近二十年来飞机设计与制造行业内的新趋势,这一革命性变化与历史上航空业涌现出的历次技术革新一样,均以军事需要为牵引研发应用新技术、新材料,在成熟并达到一定经济性后再运用于民用领域。
选用钛合金作为飞机结构件的优势有如下四点:
①结构减重。减重效果直接决定飞机综合成本的高低。钛合金比同等强度的钢的密度低4O%,用钛合金代替钢和镍基合金甚至高强度钢时,能够大量减重。
②突破体积限制。当结构载荷比较高、采用铝合金又受到结构空间限制时,强度较高的钛合金成为较理想的材料。波音飞机上采用非常大的钛合金锻件以降低结构体积,例如波音757 和747 的起落架、框、梁。
③耐高温。较高的工作温度也是钛合金的一大优势。传统铝合金仅能适用于13O~150℃,在高温区域,采用钛合金更适宜,可以提高结构效率。钢和镍基合金也可以选用,但是这两种材料密度都比钛合金大。
④耐腐蚀。钛合金具有优良的耐腐蚀性,使其在腐蚀严重区域得以大量应用。
实际上钛合金在民用飞机运营环境中,几乎不会发生腐蚀现象。在易腐蚀区域,如位于厨房和盥洗室下的地板支持结构,钛合金可取代铝合金用于连接座椅和地板。
早期制约钛合金运用的主要因素在于冶炼成本及加工成本长期居高不下,以当今世界上最为先进的战斗机美国空军装备的F22 为例,其钛合金使用比例高达41%,单机造价2009 年时1.5 亿美元,以至于美军不得不将装备数量由计划750架删减至187 架。随着冶炼及锻造技术的进步,钛合金使用范围逐渐扩大,现已成为飞机设计与制造界的宠儿。
(2)航空发动机盘件概述
航空发动机是一种高度复杂和精密的热力机械,被誉为“工业皇冠上的明珠”,为航空器提供飞行所需动力。航空发动机诞生一百多年来,主要可分为两个发展阶段:活塞式螺旋桨发动机、喷气式发动机。二战后,喷气式发动机经过涡轮喷气式发动机到涡轮风扇式发动机的发展历程逐步走向成熟,并向低涵道比的军用加力发动机和高涵道比的民用发动机的两个方向发展,现今已经成为几乎所有固定翼飞机的动力装置。同时,涡轮式发动机也演化成涡轮轴发动机,成为现代直升机的主要动力选择。
涡轮风扇式发动机主要由风扇、压气机、燃烧室、涡轮等几个部分组成,各部分均呈圆周对称状态。动力由风扇及涡轮后喷气共同提供,民航及大型亚音速飞机使用的大涵道比发动机主要由风扇提供动力,喷出的燃气仅是辅助,军用高速小涵道比发动机的动力则主要由涡轮后燃气提供,风扇作为辅助动力。
涡轮风扇式发动机的盘件主要包括风扇、压气机、涡轮及部分型号中的燃烧室。其中,风扇一般由钛合金或复核材料制作,对材料的韧性及耐腐蚀、抗疲劳性能要求较高,但对耐高温性能要求较低。多级压气机将空气压缩送入燃烧室,前部低级压气机一般由钛合金制作,后部高级压气机由高温合金制作。燃烧室产生燃气后推动涡轮,涡轮再通过转子带动前部风扇及压气机,完成进气、压缩、燃烧这一连续过程。涡轮作为发动机产生动力的核心部件,由特种高温合金通过定向结晶、锻造、镗铣等复杂工艺流程制造,需要在高温、高压、高速转动中持续工作,必须具备极强的抗震动、抗疲劳、耐高温、耐腐蚀的性能,这对材料选用及制作工艺的要求极高,因而涡轮属于构成发动机制造能力瓶颈的关键部件。
目前,制作发动机涡轮的主要材料是高温合金。一般来说,高温合金是能够在600℃以上及一定应力条件下长期工作的金属材料。高温合金是为了满足现代航空发动机对材料的苛刻要求而研制的,至今已成为航空发动机热端部件不可替代的一类关键材料。在先进的航空发动机中,高温合金用量所占比例已高达50%以上。
(3)锻造工艺概述
锻造是一种利用锻压机械对金属坯料施加压力,使其产生塑性变形以获得具有一定机械性能、一定形状和尺寸锻件的加工方法,锻压(锻造与冲压)的两大组成部分之一。通过锻造能消除金属在冶炼过程中产生的铸态疏松等缺陷,优化微观组织结构,同时由于保存了完整的金属流线,锻件的机械性能一般优于同样材料的铸件。
根据成形机理,锻造可分为自由锻、模锻、辗环。
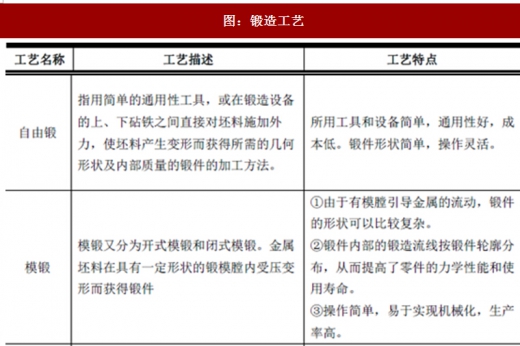
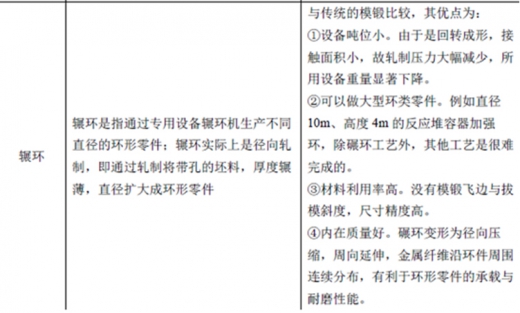
(4)航空锻造工艺与设备
现代航空工业已广泛使用钛合金、铝合金、高温合金用作为机体与发动机的主要材料,以适应现代航空器的高性能要求。由于航空用金属部件尺寸大,且对金属部件内部微结构要求高,常规的锻造、切削、镗铣等加工方法难以满足工艺要求,或者会导致废品率高、效率低下。为迎应现代航空工业金属部件的加工要求,大压力模锻液压技术应运而生。
早在第二次世界大战以前,德国为了发展航空工业,制造战斗机需要的航空铝合金锻件,于1934 年研制了70MN 模锻液压机,并于二战期间又先后制造了300MN模锻水压机1 台、150MN 模锻水压机3 台。在二战激烈的空战中,各参战方通过实战发现,模锻液压机对于空军装备的质量及生产能力十分重要。因而,二战后美苏在获得德国模锻液压机实物的基础上陆续发展研制出一大批性能优异的大吨位模锻液压机。
大型模锻液压机对于现代航空工业的发展十分重要,往往成为制约一国航空工业能力的瓶颈,甚至能直接决定某个飞机型号是否可行。例如,当今世界上最大的客机A380,其使用的钛合金起落架必须由俄罗斯750MN 模锻液压机加工,西欧尚不具备此加工能力。

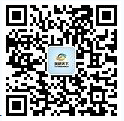
【版权提示】观研报告网倡导尊重与保护知识产权。未经许可,任何人不得复制、转载、或以其他方式使用本网站的内容。如发现本站文章存在版权问题,烦请提供版权疑问、身份证明、版权证明、联系方式等发邮件至kf@chinabaogao.com,我们将及时沟通与处理。