自润滑轴承行业发展特点
①提高产品技术含量、工作效率、可靠性和精度是大势所趋
从目前我国轴承行业产品结构来看,技术含量较低的普通轴承生产能力已较为充足;而高精度、高技术含量、高附加值的轴承,具有特殊性、能满足特殊工作条件的自润滑轴承,无论是品种还是数量都有较大发展空间。从产品质量和技术水平来看,我国每年仍需大量进口高端轴承。 提高滑动轴承生产商的研发、设计和制造能力是实现滑动轴承高技术含量、高可靠性、高效率、高精度的唯一途径。在国家政策的支持下,随着我国装备制造业的快速发展,预计未来滑动轴承行业企业将把提升轴承产品的精度、性能、寿命及可靠性等方面作为重点投资方向。我国滑动轴承制造商通过加大研发力度、引进国外先进制造设备等手段,不断提高研发设计水平及制造水平,符合未来行业发展的必然趋势。 ②根据细分市场的专业化分工进一步体现
滑动轴承特别是自润滑轴承因其用途不同,存在多品种和多规格产品。不同种类的滑动轴承对热处理水平、车加工精度、表面处理方式、生产装置自动化程度以及制造工艺等要求不同,因此现有的滑动轴承企业基本专注某一专门领域或细分市场。国际轴承行业经过上百年的发展,已经形成了稳定的专业化分工,国际轴承巨头在各自的细分市场领域组织专业化生产。如专业从事自润滑轴承生产的美国 GGB 公司、日本 Oiles 公司等。未来国内滑动轴承生产企业将进一步明确产品定位,走专业化分工道路,做强做精细分市场,实现规模效应。 ③润滑材料的研发能力对于滑动轴承设计生产起到重要作用
滑动轴承的表面材料及润滑性能决定了耐磨性、抗压性等各项性能。为了满足客户需求,不同种类的滑动轴承对于表面材料的要求不同,因此滑动轴承企业对于滑动材料的研发能力在很大程度上决定业务的拓展速度。未来滑动轴承企业将进一步加大滑动材料研发,满足生产经营需要。
自润滑轴承行业概况
(1)自润滑轴承的发展
自润滑轴承的制造技术起源于英国。20 世纪 50 年代 PTFE(聚四氟乙烯)在英国开始被作为一种轴承材料进行试验,同时铜粉烧结工艺也获得了突破。
1956 年,世界上第一个以 PTFE 作为内衬,以钢板为支撑的自润滑 DU 轴承投放市场。60 年代末,自润滑轴承开始进入航空航天等尖端科技应用领域。从 70 年代开始,英国自润滑轴承制造商将技术许可给法国、德国、日本和美国公司,这一举措推动了世界自润滑轴承行业的快速发展,自润滑轴承逐步进入到所有的机械制造领域。
(2)自润滑轴承产品的分类
随着自润滑轴承行业的发展,自润滑轴承的生产工艺和材料不断创新,产品的种类也逐渐丰富。根据产品结构和制造材料的不同,自润滑轴承划分为复层类、单层类、其他三个大类,其下分为多个子类。具体如下所示:
“复层型”自润滑轴承产品是由两种或两种以上不同类型的轴承材料层叠复合而成,其中衬层材料起自润滑作用,基材起支撑作用,其它材料起连接过渡作用。“复层型”产品的润滑效果优良,其承载能力由表面材料的抗压强度所决定。根据基材和衬层材料的类别,可分为金属基材与金属衬层复层、金属基材与非金属衬层复层以及非金属基材与非金属衬层复层。
“单层型”自润滑轴承产品是由一种类型的轴承材料制成,产品依靠轴承材料中所含有的自润滑材料如石墨、二硫化钼、聚四氟乙烯、铅等来进行润滑,根据轴承材料的类别,可分为金属类和非金属类。非金属类单层型自润滑轴承主要包括整体非金属轴承、非金属卷制轴承等。金属类单层型轴承主要包括固体镶嵌型产品与含油型产品。“固体镶嵌型”自润滑轴承是在金属基材上按照一定的排列方式预先加工出一些孔洞或沟槽,然后将固体润滑剂嵌入其中;工作过程中由于摩擦热或环境温度作用,固体润滑剂在滑动表面略微突出,并通过摩擦在金属基材和对偶表面形成转移膜,从而起到减摩耐磨的作用。“含油型”自润滑轴承是将金属粉末通过粉末冶金工艺压制烧结而成一个多孔性材料,然后在孔隙内充以润滑油;工作过程中由于摩擦热或环境温度的作用,润滑油从轴承中析出,在金属基材和对偶表面形成润滑油膜,从而起到减摩耐磨的作用。 部分 SF 系列和 JF 系列产品属于复层型自润滑轴承,其中 JF 系列产品属于金属与金属复层型产品,SF 系列产品属于金属-非金属复层型产品。公司的 JDB 系列产品是以高力黄铜、合金钢、铸铁等金属作为轴承基体材料,以石墨等作为固体润滑剂,属于单层类金属固体镶嵌型自润滑轴承。FU 系列产品属于单层金属类含油型自润滑轴承。
(3)自润滑轴承产品的特点
自润滑轴承适用于无法加油或很难加油的场所。由于特殊生产工艺的要求,汽车制造、机械工业企业的某些关键设备需要在极端工况下运行,由于设备重、环境温度高、粉尘大或空气中含酸性腐蚀气体等各种因素,难以为设备添加润滑油,因此滚动轴承或一般滑动轴承摩擦磨损严重,易发生轴承的咬伤或咬死,引起零件磨损和损坏,导致设备停运。为了生产连续运行,除在原始设计上要求安装多台设备轮修外,还须投入大量维修人员,备品备件和能源消耗极大。因此汽车制造、工程机械、模具行业等企业在复杂工况条件下都具有对特种润滑材料的需求。无油化可以使轴承设计、结构等大幅简化,降低成本,节省设计时间,可在使用轴承时不保养或少保养,也免除了由于供油不足造成的风险。通过对自润滑轴承复合材料及自润滑轴承的研究,在材料配方和制备工艺上实现创新突破,可以为客户解决特殊工况下的润滑问题。 由于自润滑轴承无需供油装置,工作过程中可以不用加油,因此可以节省大量的安装和运行成本,提高机械性能,提升使用寿命及可靠性。无油化处理无需废油回收处理,还有利于环境保护。自润滑轴承对于磨轴的硬度要求较低,从而降低了相关零件的加工难度。自润滑复合轴承结构中,表面可电镀多种金属,可在腐蚀介质中使用。此外,由于无油润滑不存在油脂挥发问题,自润滑轴承可在高温高压环境下使用。 自润滑轴承和一般轴承之间的性能比较如下:
自润滑轴承无需供油维护、耐磨、耐热等特性大幅拓展了产品的应用范围,很多普通轴承无法胜任的领域都可以使用自润滑轴承,因此自润滑轴承比普通轴承有着更广阔的发展空间。
相关行业报告参考《2016-2022年中国滑动轴承市场动向调研与投资前景预测报告》
本文来自中国报告网,转载请注明出处。
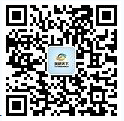
【版权提示】观研报告网倡导尊重与保护知识产权。未经许可,任何人不得复制、转载、或以其他方式使用本网站的内容。如发现本站文章存在版权问题,烦请提供版权疑问、身份证明、版权证明、联系方式等发邮件至kf@chinabaogao.com,我们将及时沟通与处理。